Hawking my skills.
- paulcqueens
- Mar 29, 2023
- 2 min read
Every now and then I'm approached about something genuinely unusual and out of the ordinary. The sort of job I enjoy most. So I was both intrigued and excited recently to be asked to take on a commission to make a traditional Falconry block, by a local enthusiast. There's a big bird jamboree in the offing, and he is keen to make something of an impact when it comes around in the summer.

There's apparently been a move away from the traditionally-made in this arena (as in so many fields), towards the cheaper far-east for manufacture, and to plastics and resins and away from wood. He was keen to find someone who could help make a 'genuine' English-wood block.
First task - understand the job in hand. So these plans from an old text-book formed the template.

Thankfully my client is a keen metalworker, so making the ring and spike fitted firmly into his remit. Having the ring 'up front' would also allow me to turn the tenon perfectly, to allow it to turn freely whilst being supported by the rest of the block.
So off to Tyler Hardwoods to delve into the offcuts sheds, and after much searching I turned up an unpromising chunk of old and well-oxidised Oak. Various splits visible (and doubtless invisible too) but as it was the only offcut of vaguely the right size, and as I was keen to avoid a bespoke cut, it would have to suffice.

Following a chat with my client, the block was cut to length and chamfered, ready to load onto the lathe.
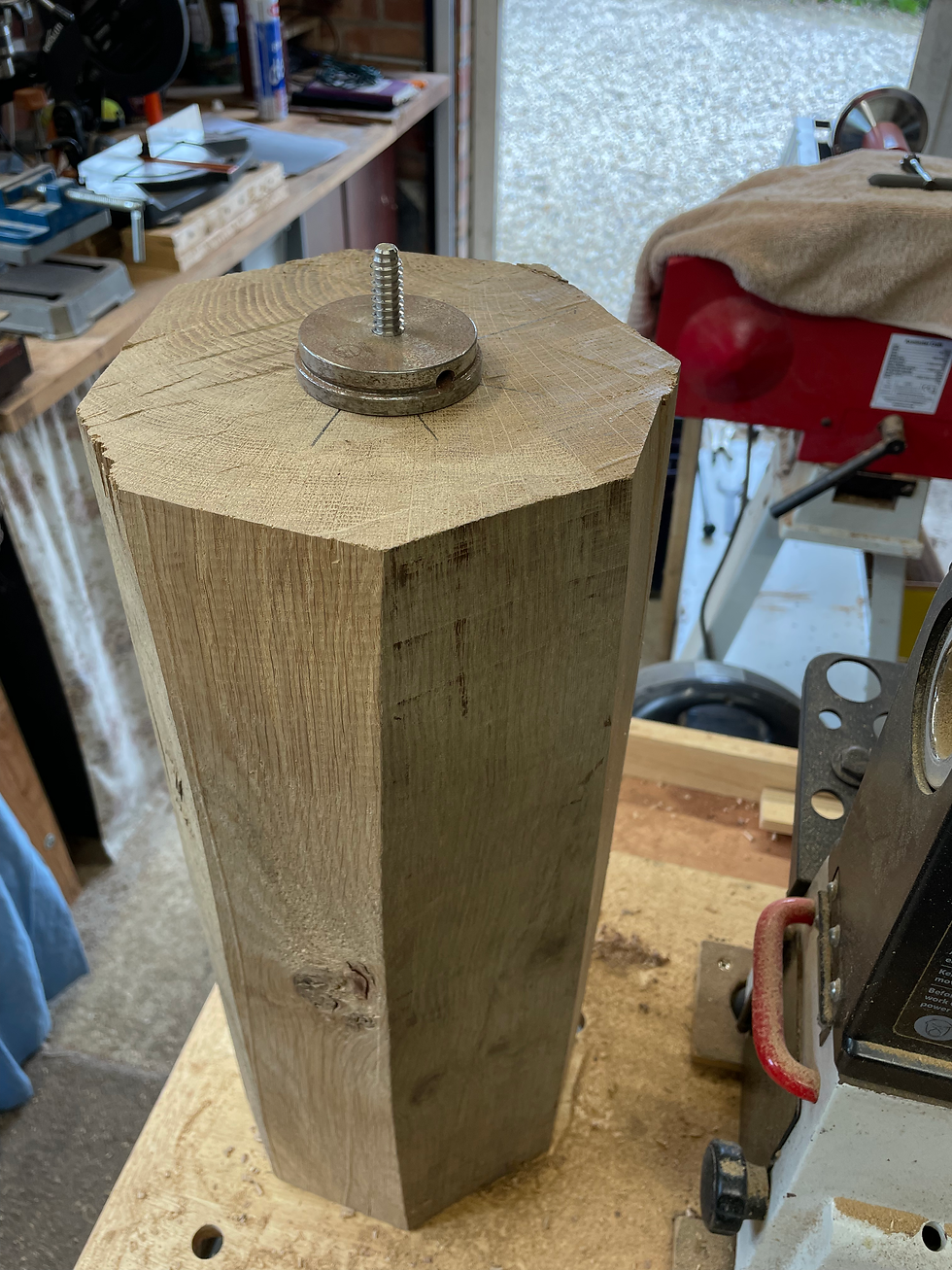
It went onto the bigger of my two lathes, and with a chuck plate firmly affixed then I felt vaguely safe at first spinning. (I've had larger chunks spin off when poorly affixed between the head and tailstocks before today, and had no desire for a piece this size to bounce around the workshop.) At a slow speed I soon managed to get it to round, and the beauty of the grain started to show through.
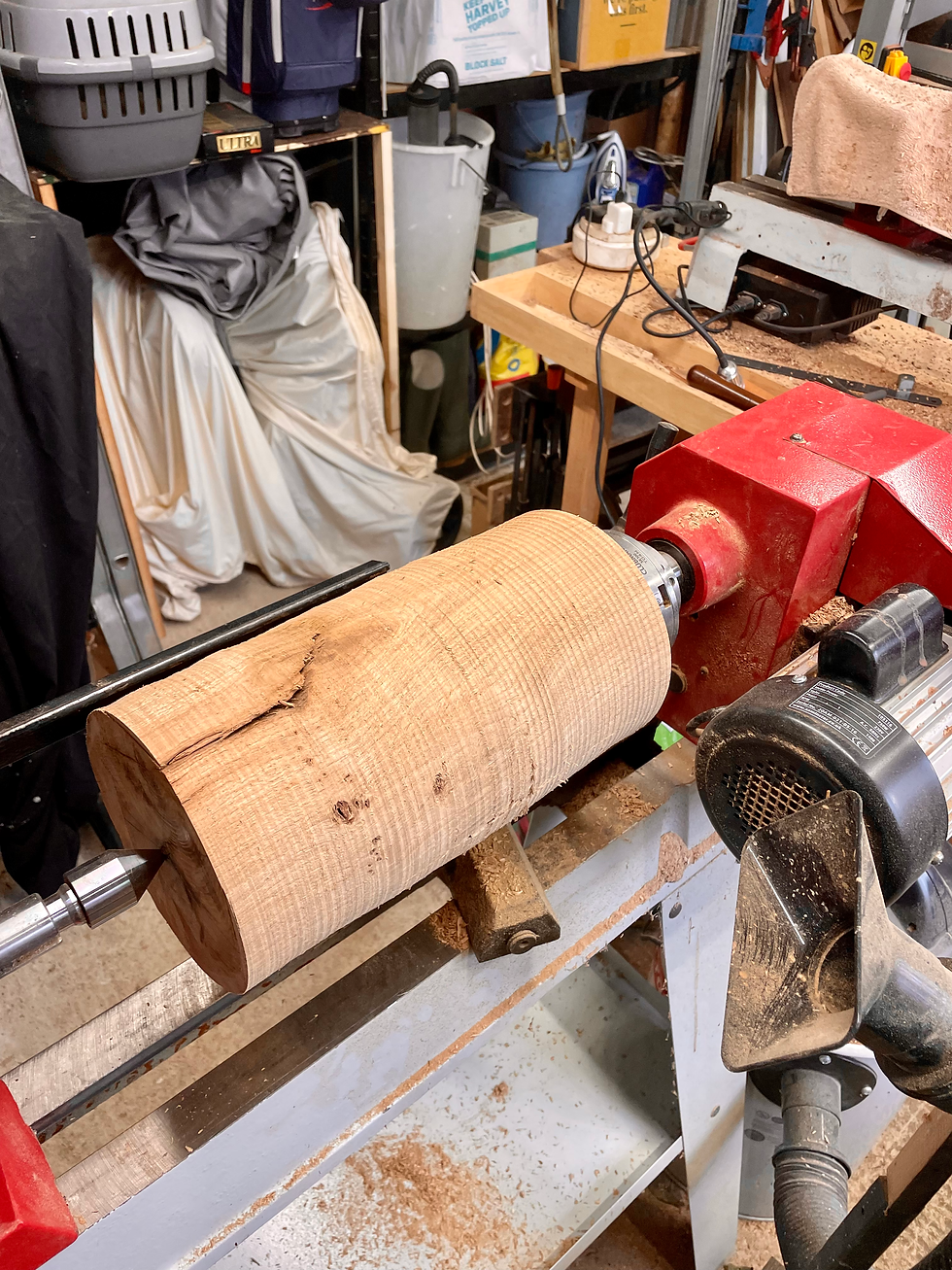
Another twenty minutes and I'd turned it roughly to its finished shape.

I'd been left with some interesting knots, in addition to a fairly ugly 'surface' split. This latter needed filling with an oak-match wood-filler, before being left to set overnight and then sanded the following day.

Now things started to get more exciting, with the creation of the 'tenon' for ring fitting, as well as some simple decorative beading at the top end.

The base was now parted from the upper section, and drilled for the spike and for dowels to ensure alignment when screwed together.

Once the dowels were set it was time to put the finished block together and deliver it to the client for finishing off with metalwork and cork top.

Since then, he's fitted the cork top......
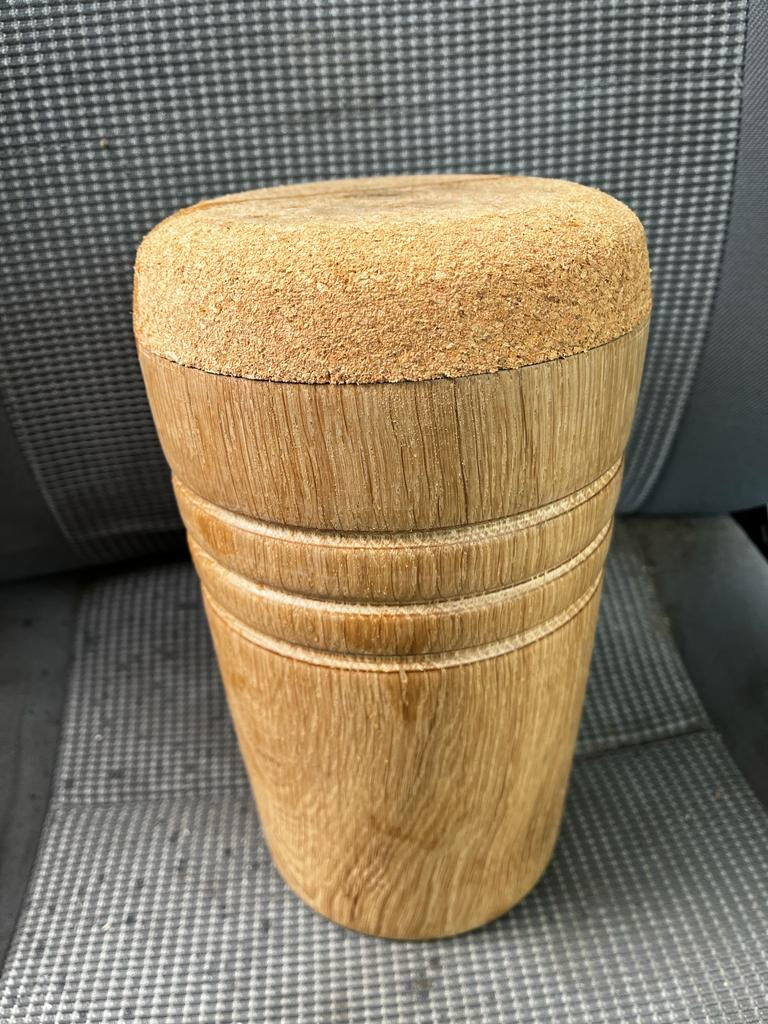
...and yesterday he introduced it to its new owner. Who was keen to inspect it for solidity and practicality.

It's been a fun job to work on, and it's a lovely piece of English oak, transformed into a beautiful and traditional object. Now I'm looking forward to seeing it in use at the earliest opportunity.
Comments